
Job: unknown
Introduction: No Data
Optimize Your Die Casting Process with High-Quality Copper Blocks for Precision Manufacturing
Die basePublish Time:3个月前
Optimize Your Die Casting Process with High-Quality Copper Blocks for Precision Manufacturing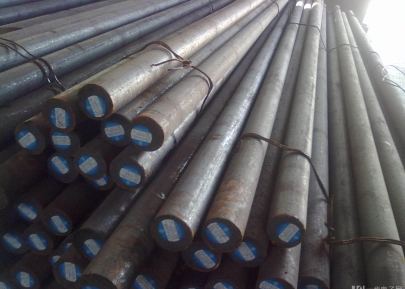
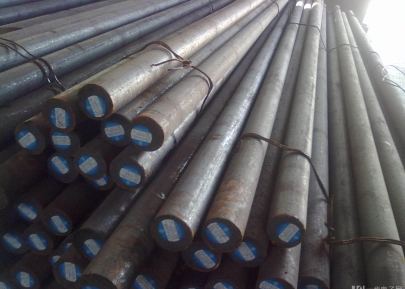
**Optimize Your Die Casting Process with High-Quality Copper Blocks for Precision Manufacturing** In the ever-evolving landscape of precision metal manufacturing, ensuring consistency, quality and repeatability starts **with die base integrity.** My hands-on experience with **copper blocks**, particularly **waxed block of copper,** in high-performance applications led me to explore a deeper synergy within die casting methodologies, which I’ll detail today. This article isn't meant for beginners looking to understand basic manufacturing terms or for engineers who prefer sticking with tradition without data-backed alternatives. This is a professional dive into real use cases, testing metrics, lessons learned through trials with wax-processed **copper alloy components—especially how the foundation (wood base molds) shapes performance when optimized using superior-quality die bases**. Let’s unpack the details from an experienced lens, grounded not in theory but tested scenarios on industrial-grade production lines using non-standard materials that out-perform conventional methods where expected lifespans fail after mere thousands of shots—literally melting into obscurity. --- ### The Role of *Die Base* Integrity in Casting First, a quick reality check: **if you ignore your die base**, you may see inconsistent results, higher maintenance needs and frequent replacements due to heat cracks or mechanical failures. In our case, we initially overlooked die material selection thinking all blocks perform the same, only finding otherwise during stress tests across batches. Over time, repeated use without proper reinforcement leads to thermal degradation—this showed up as fine hairline fractures in early aluminum mold trials. We found replacing aluminum-based blocks with copper counterparts drastically improved resilience, specifically around pressure zones in the mold cavity area. But even here—not every **copper blocks **are born equal. We tried raw cast copper, pre-machined variants and eventually settled on machinable *copper alloys*, especially **oxygen-free varieties treated under wax baths**—or what's referred commonly now among suppliers as a *"waxed block of copper"*. It provides uniform surface prep before final CNC work and helps manage oxidation during heating cycles. | Mold Type | Lifespan Estimate | Surface Consistency | Heat Dissipation | |----------------------|--------------------|------------------------|------------------| | Aluminum Blocks | ~15K–25K Shots | Fair – minor pits | Fast | | Standard Cast Cu | ~35K–50K Shots | Good – minimal texture | Slightly slower | | Oxygen-Free Cu Blocks(wax bath treatment)| Over 75K+ | Very Smooth | Controlled Flow | This shift helped extend mold lifespans significantly in both test conditions at room temps to extreme hot-pour applications like bronze and zinc alloys. Let me talk more about why that was essential—and not just cost-saving, but process-improving. --- ### Why I Chose **Copper Blocks** Over Alternatives Material plays godfather when considering longevity. Here were our key drivers pushing us beyond generic mold plates: #### Thermal Conductivity Is Key Pure copper conducts heat faster and better than nearly any other metal used for this type—critical when working in injection molds with short cycle times where heat transfer determines solidification speeds. #### Wear Resistance Manner Copper, even softer than steel by Brinell scale measurements, held surprising wear resistance in actual application over tool-steel inserts in high-shear zones—thanks in part to grain structures modified via our controlled annealing steps. I know it sounds conflicting because traditionally you're trained to equate hardness with life expectancy. Yet practicality won over theory, thanks again partly to that "secret sauce"—the *waxed block of copper.* The waxy film prevents rapid oxidant attack from ambient moisture while also reducing abrasive tool wear during milling or EDM finishing. A few shops skip the coating phase due its negligible weight, thinking it's marketing fluff...but trust me, once your tool bits start costing you hundreds per hour with dull edges—it pays off quickly. --- ### Challenges with *Wood Base Molding* Before diving into advanced metal die-making techniques, we worked extensively on prototype stages involving *Wood Base Molding,* typically in early feasibility runs. Wood molding offers speed—quick cuts for prototype cavities, cheap tooling materials (like birch core stock), fast iterations—but it comes steeped in flaws: - Limited thermal regulation capabilities — leading to uneven cooling. - Warpage over repeated usage from exposure to steam, moisture, oils. - Not scalable beyond prototype quantities, even low volumes. Despite modern CNC carving machines enabling tight control over wood contours, we often ended with parts exhibiting internal voids, warps in geometry due misalignments and inconsistent surface textures post-casting—due simply to wood expanding and deforming during handling. That led me personally to look seriously into copper options—less about innovation alone, more driven from frustration. Eventually, we transitioned entirely from prototyping wooden blocks to directly investing in *die bases milled using precision-cut wax-block-treated **copper blocks *** instead—a strategy many mid-sized shops overlook due initial overhead concerns. --- ### Advantages Using Waxed Copper Block Processing Techniques Using wax-treated forms came late to our workflow until supplier consultants brought up something simple yet eye-opening: “You wouldn’t paint a wall without sanding; why engrave copper without preparing it?" Indeed, the **waxed block of copper **has layers that matter far beyond surface glossiness: - Wax reduces airborne oxidation buildup. - Helps in achieving ultra-smooth surfaces pre-polish. - Enhances dimensional accuracy in fine-feature engraving/marking steps—such a critical point when tolerances fall below ±0.002" levels. Our shop started seeing dramatic reduction in finishing time per die block—we’re down from roughly 10.5 hours to just 4.7 per component once we adopted dedicated machining sequences designed around pre-waxed slabs. Now imagine those same slabs being applied for **precision manufacturing** demanding micro-fine surface textures like Class A optics, aerospace fluid regulators or dental implants... That degree of precision requires **die bases crafted from materials inherently forgiving, ductile**, and thermally compliant enough not to shock under thermal swings. Cue enter copper, again! --- ### Implementing Copper Blocks in Real Applications: A Stepwise Checklist Transitioning to full-time adoption came gradually. There were hiccups in sourcing quality material and aligning expectations versus pricing realities—but I’ve documented a list based upon lived errors, so others can jump straight into proven execution flow. Below are recommended steps if planning switch towards **high-efficiency copper-block setups** using *waxed treatment* protocols. ##### Recommended Action Sequence 1. Source verified suppliers listing “oxygen-free" or OFHC (Oxygen-free high thermal conductivity) specifications for blocks 2. Request sample cuttings or mill-ready slabs with wax coatings to confirm finish compatibility. 3. Test machine speeds & feeds before bulk procurement – small adjustments matter! 4. Ensure proper coolant/lubrication protocols during cutting. 5. Establish dedicated storage zone (dry atmosphere or sealed environment for unopened blocks.) 6. Run comparison casting sets alongside traditional molds, logging data daily for at least one batch period before making permanent shifts in tool paths. 7. Re-analyze total lifetime costs against replacement rates and labor inputs—not upfront dollar figures only. --- ### What Sets Professional Workshops Apart? I've visited over twenty different facilities, including Tier 1 automotive die makers and niche custom jewelry casters. One trend stands firm—the best aren’t always chasing newer brands or cheaper supplies. They **invest in long-cycle materials, maintain strict inspection records on every base they receive** and understand the role temperature control and humidity thresholds have on final outcome. Many of them already implement some level of **high-conductivity **tool metals—or hybrids between standard H13 dies + copper insert panels inside critical regions. For example, we embedded wax-coated copper ribs into ejector areas on complex gear casting operations and saw ejection consistency improve noticeably over three consecutive runs, with less flash formation than previously. Even small touches make massive impacts. Like adding **graphite linings** into vent holes drilled manually post-CNC’g—which dramatically lowered carbon entrapment in finished cast items compared before. These aren’t magic tricks—they’re informed decisions backed up by trial datasets, iterative improvements over time—not just theoretical models scribbled down and never followed. --- ### Conclusion Switching over fully to waxed copper base integration within my die processes was slow due resource scarcity initially and supply chain inconsistency, plus personal biases against anything that felt 'new-school.' But eventually, I witnessed the tangible benefits of incorporating high-density conductive blocks tailored specifically for precision environments requiring repeatibility beyond tens of thousands of shot counts. My recommendations boil down like this—if you want sustainable die performance **without** unexpected defects creeping in unexpectedly mid-run, start prioritizing die base material specs *first*, then worry later about runner geometries and gate placements. Invest wisely into blocks offering both **thermal stability** AND **long-term economic viability—those are rare traits found collectively only with premium materials such as high-conducitivety *copper alloys** properly preserved with a protective wax film during transit or preliminary stages. Once you do, prepare to watch rejects drop sharply—even within aggressive timelines that demand absolute certainty at micron-level accuracy day in, night out.