
Job: unknown
Introduction: No Data
Copper Blocks for Die Base Applications – Durable Solutions for Industrial Manufacturing Needs
Die basePublish Time:3个月前
Copper Blocks for Die Base Applications – Durable Solutions for Industrial Manufacturing Needs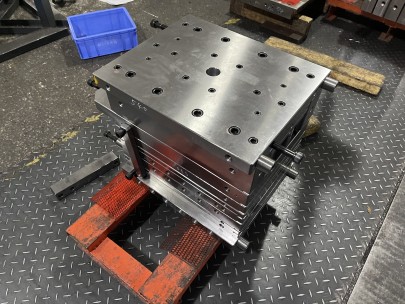
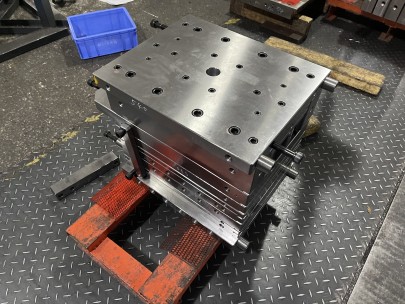
**Article Body Content Starts Here:** 当 I first starded working in industrial manufacturing, one component that stood out to me due to its importance—and yet seemed undereestimated—was the copper block used in die base applications. Initially dismissed as just a small mechanical element, I realized how critical and complex its function was, especially under demanding environments and high-performance expectations. --- ### **Understanding What is a Die Base?** (H2) The foundation for stamping tools and forming systems often lies in well-engineered *die base* construction. A die base consists primarily of a sturdy housing or mounting structure made up from materials chosen with purpose—not randomly selected but calculated based on operational demands. The most suitable candidates are metals that offer longevity against repeated stress, precision tolerances and structural rigidity—copper comes into play here more than you'd imagine. Copper has become an ideal choice due to its unmatched balance of thermal conductivity, resistance to corrosion, and machining friendliness, particularly when integrated with die components designed for specialized use such as those found within automated metal-stamping setups. While steel tends to dominate discussions around tooling materials in this niche industry (as seen during visits across various facilities in Detroit), engineers and technicians are slowly warming to copper as part of die bases that require less downtime due to overheating issues or electrical resistivity complications. --- ### **Why Copper Blocks Matter for Performance in Toolmaking (H2)** One aspect that kept resurfacing whenever discussing production challenges with veteran toolmakers was about signal integrity. You've possibly asked—like so many before—I did—"does copper block cell phone signals"? Well, partially—yes. More specifically, copper is known for disrupting EMF (Electromagnetic Field) transmission—especially at specific wavelengths. This can lead to minor disruptions in connectivity if improperly insulated near sensitive sensors on automated equipment (think IoT-controlled press units in Tier One automotive manufacturing). Now why would copper even matter beyond durability in tooling? Here’s where it gets intriguing for people like myself who’ve worked extensively within automation plants where CNC control units run day & night: copper integrates not just structurally in mold frames but electrically too! In modern settings like ours—a hybrid facility in Cleveland—copper acts dualistically—as mechanical strength while also functioning like EMI (Electromagnetic Interference) shielding when placed adjacent to circuit housings or power relays. In short: - Copper improves electrical grounding points. - Enhancing system reliability in noisy industrial atmospheres (from weld stations to high-frequency laser markers). - And crucially—if not managed well—it can interfere with wireless diagnostics if left uninsulated. So next time you comeacross an old technician mumbling about his tablet losing connection next to certain tool chests—there’s science involved, not sorcery! --- ### **Selecting Quality Materials for Die Systems (H2)** There aren't many off-the-shelf products ready for use inside our factory. Most material specs come directly from engineering blueprints developed alongside R&D teams in Michigan or Illinois plants. For die systems involving copper elements, three core properties drive decision-making: **1. Thermal stability** – prevents localized deformations from heat buildup. **2. Machining flexibility** – essential in crafting tight-fit blocks with minimal tool wear **3. Reusability & Repurposing capability**– important during prototyping phases where adjustments happen multiple times. To simplify comparison for procurement folks—or DIY manufacturers considering upgrading shop-level infrastructure—the table below illustrates typical material traits: | Property | Steel | Cast Iron | Copper | |--------------------------|-------------------|-------------------|----------------------| | Thermal Conductivity (W/m°C) | 45 - 60 | ~80 | **>390 highest** | | Electrical Conductive | Fair-Limited | Very Poor | Outstanding | | Weight | Heavy | Moderate-to-high | Medium | | Cost Per Unit @ Supplier | High | Low to moderate | Variable / Premium* | > Note*: Depending upon whether you select beryllium-copper alloy blends for custom-mold inserts. --- ### **Vinyl Base Molding Applications: Surprising Use Cases With Metal (H2)** When exploring unconventional uses of conductive copper alloys outside of traditional machinery, a fascinating tangent appeared—a trend among architectural fabricators adopting vinyl-based substrates with embedded thin-layer copper strips acting almost like heating mats beneath plastic flooring in residential zones (particularly northern states during snow months). I came across an experimental project led by design firm near Boston trying to integrate smart-heated floor prototypes using recycled polymer compounds layered onto metallic grids including stamped copper profiles derived from leftover die molds—reused no less! What started out seeming odd—metal plus molding in homes? But there are clear advantages: 1. Efficient radiant energy conversion via ultra-thin copper layers 2. Easy installation compared traditional wire systems (faster ROI) 3. Reduced long term maintenance headaches—copper does degrade minimally unlike carbon sheets So for designers curious, copper might soon appear less foreign beside their **vinyl base molding designs**, offering new dimensions both aesthetically and in performance terms—provided they collaborate with engineers early-on, not later! --- ### Key Takeaway From My Years Handling Production Lines If nothing else sticks with you about my experiences over these several seasons of troubleshooting plant floor operations, let me summarize a quick checklist: 🔍 Always assess the intended environment where your die block operates. ✅ Copper performs poorly only when used incorrectly—without consideration of insulation strategies or EMI interference zones near sensors. 🛠 Partner closely with local vendors or casting shops that offer customized solutions instead default stock materials—often the case in mid-west USA. 🌐 Ask your peers "has anyone tested if copper blocks WiFi nearby" before finalizing machine layouts—because sometimes, you find yourself repeating past mistakes otherwise easily avoided through collective insight. Don't take chances with unknown materials. Stick proven ones—copper included—but always understand *why it's right for that specific job,* rather than copying someone else without analysis. And lastly... 🧾 Create standardized evaluation forms whenever selecting blocks going into future mold designs; here's what I carry: #### Essential Copper Evaluation Checklist - [✓] Thermal management requirements assessed - [✓] Conductivity profile verified with vendor spec sheets - [ ] Environmental compatibility test data reviewed for humidity/salt-spray levels (critical coastal facilities!) - [ ] Physical tolerance dimensions aligned with current jig setups - [✗] Cross-checked with IT department to identify potential communication risks from installed material (surprisingly easy fix overlooked too often) As trends change—from robotics replacing conventional setups to AI monitoring predictive failures—you’ll find the basics still count. Even ancient metallurgical principles—hundreds year old now—find fresh applications today thanks to evolving tech stacks demanding more integration between hardware disciplines. Don’t ignore copper; revisit it thoughtfully each design phase. Until next article, — *[Author's Name Hidden]* – An industrial systems specialist from Midwest U.S., always tinkering. **Conclusion (Final Recap)** In wrapping up what started as exploration into humble copper pieces tucked away inside hardened machinery structures—it became apparent these blocks do a lot more than just endure pressure and repetitive impacts. Whether serving as durable platforms for heavy-duty punch/die combinations, playing key electromagnetic buffering roles around digital controls—or branching out quietly into novel building sectors like warm vinyl flooring—the role of copper remains far more versatile than initially expected. Choosing correctly requires deeper inspection beyond cost-per-pound or availability, though those definitely factor in eventually. Understanding *application needs*, matching physical attributes accurately—and collaborating smarter than competing alone—are what elevate any engineer toward lasting professional impact. Whether you're outfitting an Ohio assembly line, testing smart flooring prototypes in Vermont—or merely wondering whether to toss a cheap copper ingot into your junk drawer—I hope these insights serve you well moving forward!