Introduction
When it comes to manufacturing high-quality copper components, I've spent years exploring how the foundation — particularly the mold base — plays a crucial role in determining end quality. In my experience, starting from block of raw copper may look straightforward, but the subtleties of choosing or designing your mold system can't be over emphasized. This article isn’t your standard guide you might find online — we’re diving deeper into real-world usage, with some insight on Base Molding Wood, while addressing questions like if and when you're likely to ask “does gold plated copper tarnish."
---
Understanding Mold Base – What Really Makes It So Crucial?
- Critical Role: A proper mold base supports precision machining by ensuring stability, alignment, and repeat cycles.
- Machinability: I’ve found that mold bases made from high-grade materials ensure smooth operation with blocks as rigid as raw copper billets.
- Balanced Load Distribution:If using raw material like block of raw copper, thermal conductivity needs a strong and evenly structured mold support underneath—especially during injection and press-forming stages.
If you’re just beginning to explore metal forming systems like copper forging, you might question why a mold base deserves this deep exploration.
Digging beyond surface logic, what becomes evident is that mold bases not only bear physical and thermodynamic pressures but also serve as foundational structures where tolerances, heat distribution, and structural rigidity meet under heavy force loads. ---
The Raw Material’s Role — How Blocks Affect Molding Outcome
Aspect of Block |
Impact on Mold Design |
Common Issues Faced |
Shape Uniformity |
Influences cavity layout; inconsistent shape means unpredictable cooling time |
Warping or distortion after molding |
Density Consistency |
Pure vs composite affects melt uniformity during processing stage |
Bubbles or cracks inside cast piece |
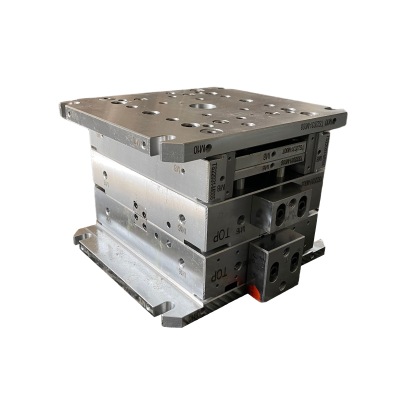
Starting with raw block copper, one must account for natural variability—be it minor impurities, internal stress lines, etc. That’s where pairing your mold structure accordingly is more art than process. Many newcomers to die-making overlook the synergy here between base materials, pressure settings, AND the integrity of incoming stock—here's what I wish someone told me ten years ago…
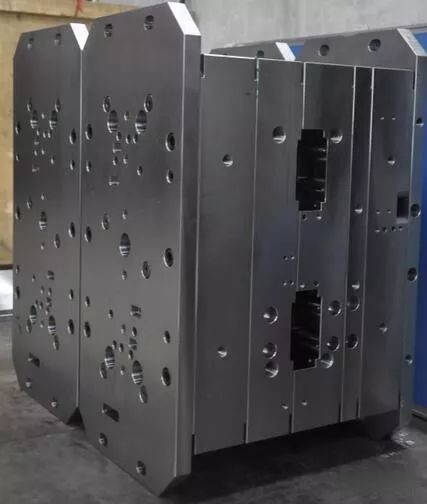
The key is not to think about "blocks of copper" as inert elements. Each slab carries potential stresses from its creation and shipping. These factors impact dimensional consistency down-stream during casting steps involving mold bases.
---
Choosing the Right Materials: Does Mold Wood Even Fit Into This Picture?

Wait — am I mixing apples with oranges mentioning **base-molding wood**? Let’s address that honestly: in prototyping and low-rate preproduction, many engineers still use what we call 'pattern-grade' wood such as beechwood for early mold testing, especially when cost-efficiency takes priority. However... In long-run industrial settings (which is what we're aiming toward here), actual wood-based options have minimal role due to wear rate and dimensional drift—but in small operations handling
custom-forged copper elements or test forms starting out with raw slabs — yeah, sometimes I’ve done preliminary tests using
Base Molding Wood because CNC milling wasn't worth initial expenses yet at prototype stage. Key takeaway? Understand context. ---
Tackling a Curious Question: Will Gold Plated Copper Oxidize?
It always happens: I'll be talking about alloy choices with folks who handle high-conductivity copper, and sooner or later someone pops up with “Does gold plated copper tarnish?" To be clear, pure **raw block copper** is vulnerable oxidation and green verdigris appearance overtime — especially under moisture and sulfur environments. When plated with precious metals however, this behavior slows. Here are some points based on personal observations:
The layer of gold acts primarily protective, provided it is uniformly applied without pinholes or microscopic fractures. But nothing lasts forever. If environmental conditions get hostile... - Moisture + salt = increased risk factor - Constant abrasion will thin plating over time — making under layer exposed to atmosphere again. - Sudden changes in temp/humidity cause condensation pockets leading to eventual micro-rusting at seams But let's keep realistic. Most gold-plated setups exist in electronics, connectors, PCBs and decorative hardware rather than extreme industrial zones. Hence, degradation may appear less frequent in daily life scenarios—but it’s there silently progressing, unless maintenance checks prevent it ahead-of-time. ---
Molding Techniques: From Theory to Real Application
Now, onto actual implementation: What follows is an approximate process outline — tailored for working directly from
block raw, whether through extrusion methods or forge-hammer routes, each demanding specific mold configurations. My favorite method has become hot forging via semi-closed mold sets anchored atop vibration-damping surfaces — this combination offers better edge retention & grain structure preservation within processed copper parts, which translates higher durability once installed. But don’t take my words as gospel... I’ve seen colleagues prefer open die rolling for elongated shapes and cold press tools for fine engraving / stamp detail applications. Let your part dictate form and material flow path. ---
Mold Base Considerations You Should Not Ignore
Here’s a list based upon practical experience, not technical manuals — the kind stuff they often forget teaching you until something breaks mid-shift. - Avoid mismatched hardness profiles in mating base-to-core sections — this creates localized wearing spots. - Never install molds directly on unconditioned concrete. Vibrational resonance kills both lifespan & accuracy fast! - Pre-staging your
mold bases helps catch early misalignment even before raw block hits production floor. - Cooling efficiency starts well below visible level — consider dual-phase fluid routing built into mold frames for faster extraction and better finished component properties. One thing people ignore entirely until late-stage failures: regular
sinkhole detection tests on the mold itself. Especially critical if your raw feedstock contains uneven composition areas which could leave weak regions behind once solidified inside molded cavities. ---
Conclusion: Getting Every Step Right
Working with mold base systems demands understanding far beyond their physical dimensions. It's interplay between materials — raw copper blocks being merely one component in complex dance of pressure dynamics and thermal management. Whether selecting tool-grade plastics instead, experimenting with wood prototypes during early builds, managing plating integrity against tarnish risk, or simply refining setup before final casting phase — every tiny variable stacks to produce outcome. At the end though, success isn’t just about knowing how a mold should work technically — it's also knowing when to step back, assess your own mistakes, adjust practices based on reality, not just specs. If your goal aligns with mastering consistent output, especially when starting with high-purity metallic slabs, the insights provided should serve both beginner journeyers as much as experienced moldmakers seeking refresher reminders grounded in field reality rather than ideal conditions. After all...we've learned through trial—and lots of it, trust me. ---