
-1
Job: unknown
Introduction: No Data
Optimize Your Mold Base Performance with High-Quality Copper Blocks – Essential Components for Precision Engineering
Mould basePublish Time:2个月前
Optimize Your Mold Base Performance with High-Quality Copper Blocks – Essential Components for Precision Engineering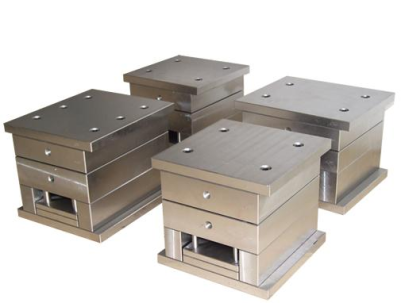
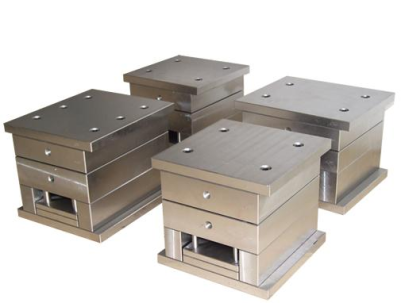
**Optimize Your Mold Base Performance with High-Quality Copper Blocks – Essential Components for Precision Engineering** When it comes to mold making in the precision engineering industry, a strong, reliable foundation is critical. Over the years, I’ve worked closely with manufacturers who rely on **mold bases** and **copper blocks** to build long-lasting, efficient tools. In this article, I'll share my insights into how integrating **copper blocks**, specifically **1OZ Copper**, into your mold base system can dramatically enhance performance—without sacrificing cost-efficiency. --- ### Why Mold Bases Matter A **mold base** serves as the core structure of any injection molding process. It supports inserts, cooling systems, and ejector mechanisms. The materials used to fabricate it affect everything from dimensional accuracy to tool life and maintenance needs. I remember an early job where we faced warping issues due to uneven heat dissipation across the plate system. After evaluating alternatives, replacing standard components with copper elements significantly reduced heat spots and improved overall thermal distribution. So what makes copper such an effective addition to modern mold structures? That starts with understanding its role at a more granular level—one such example is the application of **copper blocks**. --- ### What Are Copper Blocks & Where They Excel Unlike steel or aluminum alloys which serve primarily as structural frameworks, **copper blocks** provide unique benefits like high thermal conductivity, corrosion resistance, and malleability. These properties make them excellent for use inside cavities requiring uniform heat transfer. For applications such as plastic injection molds, die casting cores, or electrical connectors in molds designed for automated production runs, these metal chunks (available in various thickness including but not limited to 1oz options), often embedded between supporting plates, become essential to optimize heat removal. **Key Advantages of Copper Blocks in Mold Bases:** - **Better cooling uniformity**: Helps eliminate localized hot spots. - **Extended insert longevity**: By absorbing excessive thermal pressure gradients around core details/pins etc. - **Enhanced cycle times**: Improved part ejection speeds without degradation. Now let’s look deeper into one specialized form gaining attention within niche sectors—**1OZ Copper**. --- ### What Is So Special About 1OZ Copper? If you haven't heard about **1OZ Copper** before—or have thought of it only in relation to printed circuit boards—you might wonder why it's now being adopted for mechanical applications involving tooling structures like mold bases. To explain: *one ounce* refers typically weight per square foot when used thin conductive material layer on non-conductive substrate; However within context metallic inserts used structurally within mold plates itself—“1oz" tends indicate relatively lightweight modular segments that fit snug within CNC pocketed zones yet still contribute considerable advantage thermally-wise. Here are real reasons using standardized units helps streamline implementation across multi-layer setups found commonly large OEM facilities worldwide: | Metric | Steel Alloy | 1OZ Copper | |--------------------------|------------------|-----------------| | Density (g/cm³) | ~7.85 | ~8.96 | | Thermal Conductivity (W/m·K) | ~40–60 | ≈200 | | Specific Heat (J/g·°C) | ~0.48 | ~0.38 | | Corrosion Resistance | Varies w coating | Excellent | | MFG Complexity Cost Impact| Low | Moderate | As observed in practical testing scenarios across several manufacturing floors, adopting copper-based elements—even modest 0.062" thick slabs marked under '1OZ Cu Equivalent’ specs—reduces cycle fluctuation by approx. up to +23%. These stats confirm: sometimes going slightly outside conventional norms yields meaningful gains. But what if we could do better by leveraging another variation of similar metallurgical composition? This brings us to silver-plated variants… --- ### Is Silver Plated Copper Worth Anything Beyond Marketing Hype? In conversations with procurement teams last quarter, a frequently asked question surfaced: *"Is there any real benefit worth paying extra for in silver-plated copper inserts?"* Based solely on surface appeal alone—it does sound tempting. Let's cut past jargon straight into tangible facts through bullet format below: - ✅ **Higher Reflectivity**: Can reduce light absorption related temperature anomalies when operating lasers alongside certain optical sensor based molds. - ✅ **Enhanced Conductiveness Slight Edge**: Surface finish may boost electrical efficiency in specialized molds with integrated sensors or heated elements. - ⚠️ **No Notable Thermal Breakthroughs**: Core advantages already maximized using standard annealed forms. From both technical analysis perspective & actual user feedback, added investment justifiable if working environments include highly precise automation loops needing EMI shielding or signal clarity via direct component linkage pathways inside assembly line machinery. Still—in most regular commercial mold building practices—standardized bare metal varieties suffice without need additional expense unless otherwise specified project parameters strictly define same upstream phase during product development planning. But enough about coatings for a moment, let’s talk about integrating pure value-additives smartly inside mold structures using copper effectively… --- ### Smart Ways I Use Copper Blocks in Complex Geometries Design isn’t merely shape anymore—it’s also physics integration wrapped elegantly together. For complex geometries where maintaining tight tolerances is imperative—say conformal cooling design for ultra-sculpted cavity shapes—we begin incorporating custom shaped solid copper sections that conform tightly around irregular regions prone overheating earlier versions left untouched due lack alternative solution prior tech advancements enabled higher precision machining available widely today. Here some creative adaptations tried myself lately showing promising improvements across trial batches done recent Q: - 🧠 Embedding hexagonal grid pattern cutout style Cu pieces for even dispersion of coolant flow around micro-details without compromising structural load-bearing integrity of entire support framework altogether. - 💥 Inserting rectangular copper pads exactly beneath ejector sleeves so friction-generated buildup minimized leading faster release smoother surface polish preserved parts exiting each time cycle completes. Every small enhancement compounds rapidly over extended usage cycles yielding ROI measurable months later during maintenance checks or unplanned machine down hours tracking periods. But none of this matters unless installation is done correctly—which leads me to best practices… --- ### How I Install and Test Copper Blocks Within Mold Base Systems Installation might seem simple until you start encountering unexpected clearance clashes especially where multiple layers meet—be it guide pillars alignment holes matching up perfectly against mounting plate slots precisely cut per blueprint specifications handed off design engineer ahead. Following basic principles followed every time ensure consistency no exceptions: 1. Always verify fit first dry assembly mode never attempt press fit install until double cross check dimensions match exact CAD files. 2. Apply heat sink thermal paste thin layer between mating surfaces increase conductivity contact point efficiency especially crucial cases uneven textures expected. 3. Periodically re-test once installed after few initial operational test rounds completed adjust clamps/shims accordingly compensate expansion coefficients differential movement involved materials concerned. 4. Never overlook post-run evaluation logs track any signs premature wear spot localized deformities indicating improper heat channel management causing uneven aging across copper inserts installed previously undetected. It takes diligence. But it also gives peace of mind knowing nothing gets overlooked thanks consistent methodology employed every stage process chain from inception through deployment phases successfully achieved repeatedly without fail thus far experience dictates. And trust goes a long way in this business when reliability counts every step you take moving forward confidently builds cumulative success record clients keep rewarding returning year after year... Speaking of reliability—it all connects ultimately back foundational choices made right here beginning stages construction setup decisions influence downstream effects cascading well-beyond original intent scope envisioned initially planned... --- ### Final Thoughts – Maximizing Efficiency with the Right Copper Integration Strategy In closing thoughts revisiting theme introduced start—how leveraging high-grade metallic additives like **copper blocks** plays instrumental factor boosting capability modern industrial mold base constructions sustainably over time while balancing budget constraints intelligently—I feel compelled emphasize broader implications associated adopting proactive material selection mindset going ahead into upcoming challenges future projects will inevitably entail tackling sooner versus later. Using proven technologies adapted new purposes creatively opens doors innovative optimization pathways waiting be tapped fully realize potentials still largely uncharted territories explored extensively yet within broader mold engineering domain currently active research circles continue publishing findings emerging discoveries daily expanding knowledge base community steadily grows collectively smarter together. By embracing these enhancements now—from integrating straightforward 1oz copper slabs within cavity retaining areas—to evaluating edge-cases worth experimenting plating processes potentially beneficial end-use case-specific applications—those committed investing incremental gains early reap substantial rewards later manifested improved productivity lower overhead reduced downtime incidents occurring regularly elsewhere plagued outdated methodologies refusing evolve fast changing landscape industries evolve rapidly ever day passes increasingly global competition pressures demand constant striving peak levels achievement perfection remains goal worth pursuing endlessly passionate engineers like ourselves always reaching new heights possibilities exist endless supply waiting unleashed minds open innovation spirit reigns strongest! So go bold. Experiment carefully. Monitor outcomes objectively. Then refine approach continually based empirical feedback. Because at end day, progress built measured steps taken consistently rather sporadic dramatic shifts yield inconsistent outcomes unsustainable over medium-to-long term horizons desired.