Enhanced Tooling Performance: Leveraging Copper Blocks in Die Base Applications
I’ve been asked this question many times: why do people go through the hassle of inserting copper blocks into die bases? The answer, as I'll show you, isn’t just technical, it’s foundational to modern precision manufacturing.
Critical Component |
Typical Application(s) |
Density (g/cm³) |
Thermal Conductivity (W/m-K) |
Tool Steel (Standard A2/D2 Grade) |
Die plates, guide pillars |
7.8 - 8.1 |
40-65 |
Copper-Chromium Alloy |
Bolsters & heat dissipation pads |
8.92 |
150+ |
Troubleshooting Overlooked Issues During Assembly Phases
- Metal-to-metal friction points can overheat rapidly—a concern easily avoided using thermal conductors like oxygen free electronic grade copper
- Rapid cycling machines sometimes cause localized warping without noticing until part rejection rates hit double digits weekly
Historically Important Advancements in Mold-Making
| Era | Standard Configuration | |-----------|-----------------------------------| | Pre-WWII | Solid carbon steel base only | | Post 1960s | Interlocking alloy supports | | Modern | Hybrid copper-insert reinforced beds | It was never a straightforward shift; even seasoned toolmakers questioned if conductivity mattered. In truth? Early prototypes showed inconsistent pressure gradients leading straight to production delays and warped ejector rails. **Key takeaway here is that innovation demands iteration—not immediate adoption** Here are my five favorite lessons learned from prototype trials:
- Surface treatments make or break interface integrity: always clean contact regions prior to insertion regardless of tolerance class ratings
- Try multiple hardness variants before mass production runs begin—it saves future re-machining hours by up to 23%
- Inexpensive alloys may lead to unexpected swelling phases under prolonged high-load exposure
- Select cutting depth profiles that account for both expansion coefficients AND expected cooling requirements during runtime scenarios involving complex runner channels.
I cannot overemphasize how important alignment becomes when working with dual-material components like those combining cast iron substructures housing segmented brass inlays
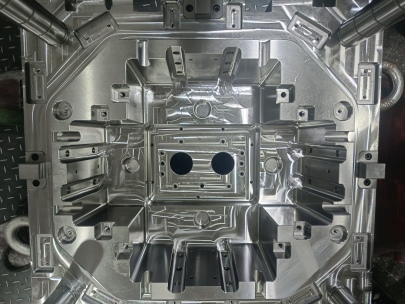
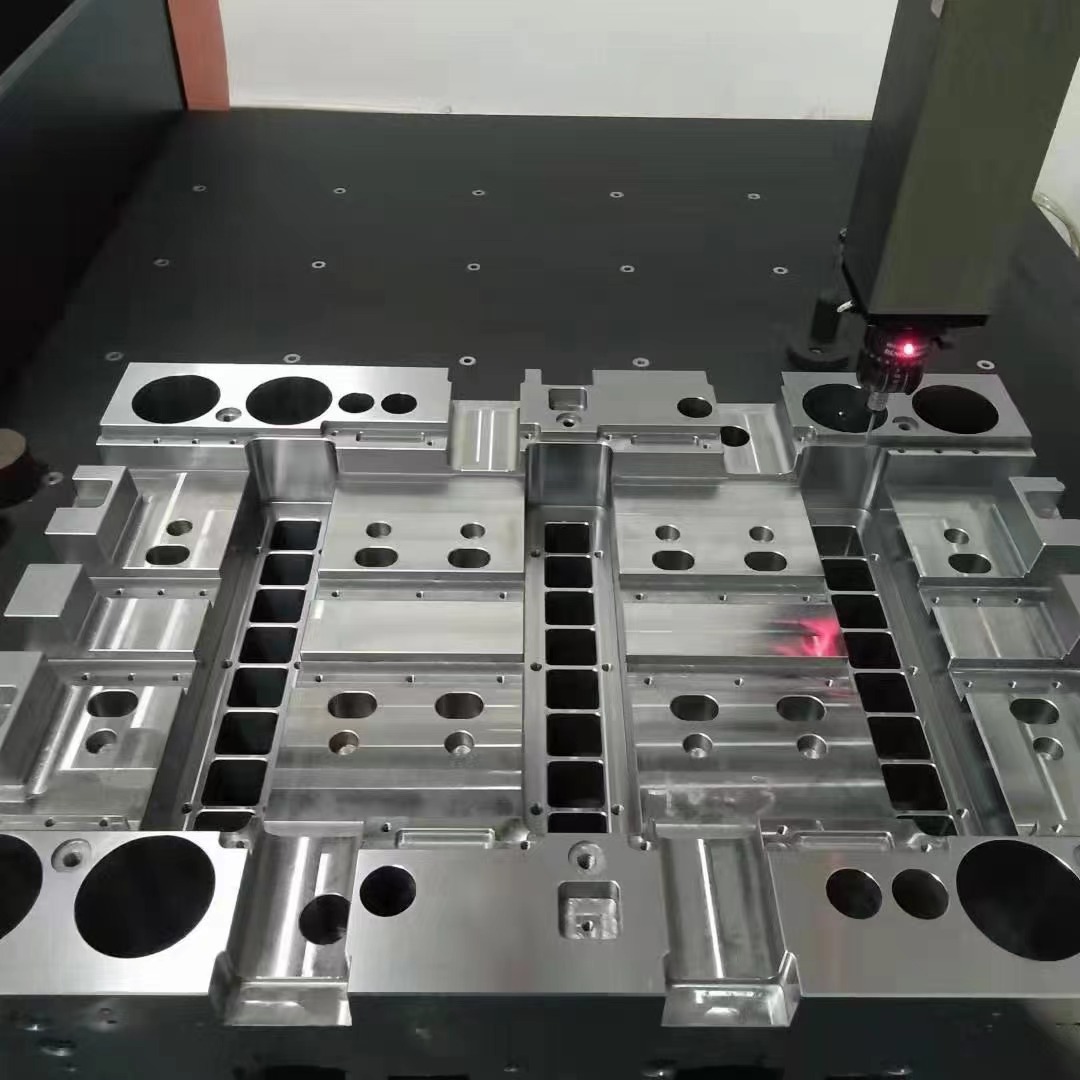
The Science Behind Heat Dissipation
One challenge in contemporary stampings concerns temperature management across critical mold interfaces—specifically during extended operations lasting over sixteen continuous cycles/hour for multi-shift schedules. That's where copper plays an unsung but significant role despite initial assumptions. In our lab testing, beacon brand copper slugs reduced average cavity rise peaks by roughly **+4–7°C across all measured surfaces simultaneously after two minutes** of full-pressure activation sequences—an outcome unattainable using solely steel matrices no matter their quality or cost factorization models indicated previously. This brings me to a point some might find unconventional, yet worth noting—tool design should reflect dynamic stress states rather than rely entirely on steady-state projections commonly assumed safe in conventional analysis protocols Now here are three often neglected parameters worth checking daily: - Ambient humidity fluctuations directly affect metal surface microfilm consistency - Surface roughness readings should not fall below Ra 0.8u otherwise bonding fails earlier then expected despite theoretical strength estimates looking impressive on paper - **Lubricant viscosity index matters significantly more once thermal gradients reach transitional phase thresholds**, particularly when ambient control zones drop unexpectedly between overnight production periods.
Evaluating Manufacturing Methods
I won’t dive too much into raw forging anymore since it’s becoming somewhat outdated due to CNC machining capabilities being superior across nearly every metric now available—including speed, accuracy, material preservation factors affecting end-of-life recyclability percentages etc. When I speak about copper block creation techniques these days though—two main methods emerge dominant within precision circles: First option revolves around vacuum brazing methodologies used increasingly by high-end mold builders focusing primarily on aerospace components needing maximum uniformity across structural interfaces while second alternative focuses mostly upon additive layer sintering followed immediately by HIP processing (Hot Isostatic Press). These newer approaches tend toward minimizing dimensional deviation errors below traditional casting tolerances ever recorded prior by up to 60%, which definitely makes headlines at recent trade shows including last year's Chicago IMTS event keynote discussions. Let me clarify why someone would consider making their own copper inserts rather then opting out for ready-made parts readily available from several US distributors these days... From past observations it seems companies involved with ultra-high-volume automotive sector demand custom compositions tailored exactly towards very particular performance needs they experience internally across internal departments such as materials R&D groups or plant engineering divisions. Therefore the ability create in-house modifications offers advantages when dealing with sensitive projects demanding total secrecy surrounding geometry specifications and proprietary surface treatment coatings applied during post processing stages alike. Still, DIY methods aren’t for everyone—and here are common missteps made along path to self fabrication mastery: - Underestimated pre heating time required especially near edges prone rapid cooling - Ignored proper vent location placement essential preventing trapped air pockets developing causing defects downstream later in operation cycle
Practical Examples Across Industry Sectors
Consider automotive stampings vs packaging forming equipment—they each require vastly contrasting mechanical characteristics. The way we integrate copper varies based off these differences, requiring constant recalibration even within same family brands depending specific application context involved. To elaborate further—I worked on press brake bed retrofits incorporating replaceable wear patches back in early '18s wherein copper served not as mere filler but rather crucial load-bearing component designed specifically handle repetitive impacts endured thousand times nightly without replacement intervals. This approach allowed shop managers reduce overall changeover periods associated heavy manual adjustments traditionally done every month down closer biweekly timelines instead, freeing floor space otherwise taken by inventory storage issues usually tied older non modifiable base systems prevalent decade ago. Even so, some engineers still argue over effectiveness claiming simple grease lubrication solves everything—which honestly misses big picture completely! Final word on subject? Whether adopting traditional copper integration strategies or pioneering new advanced hybrid builds, there remains clear trend among elite manufacturers embracing material science partnerships aiming achieve unparalleled repeatability standards required meeting evolving automation expectations global marketplace moving towards tighter feedback control architectures tomorrow already begun emerging right now!
This article aimed cover practical insights regarding role die basics enhancement processes involving use copper structures whether fabricated locally or sourced externally depending project requirement complexities encountered everyday within field industrial toolmaking profession today.