Metal | Tensile Strength |
Elongation % |
Hardness (BHN)~ | Thermal Conductivity (W/m-K) | |
---|---|---|---|---|---|
1 | OFE Copper - C10100 | >15 | >40% | 40-50 | 390 |
2 | Copper C110 | >20 | >30% | 40-70 | 370–410 |
3 | C18100 – Chromium Cu | >50 | > 25 >% |
75-95 | 350 |
4 | CuBe2 (UNS C17200) | 125 | < 20 | 250–310 | 330 |

Job: unknown
Introduction: No Data
Optimize Your Die Base with High-Quality Block of Copper for Precision Manufacturing
Die basePublish Time:3个月前
Optimize Your Die Base with High-Quality Block of Copper for Precision Manufacturing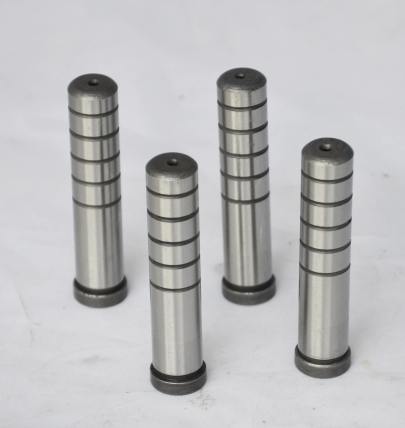
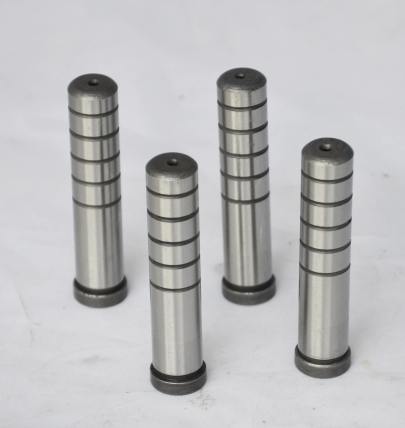
**H2: Introduction to Copper Components for Die Base Optimization** As an experienced machinist with decades in toolmaking environments, I've seen the die base evolution—from makeshift setups built on cast iron and low-end alloys to finely-tuned steel platforms augmented with precision copper inserts. Among the many advancements in modern precision manufacturing, block of copper utilization remains undervalued by many, including seasoned pros. The reason why many neglect quality copper blocks for sale often comes down to a basic misconception: copper simply "carries heat," which is only half-truth. It *stores,* *channels,* and even regulates temperature depending on its grade, grain composition, and application. This subtle complexity is critical when optimizing your die base—especially when working high-heat or ultra-precision operations involving welding techniques and tight tolerances. So, whether sourcing from established manufacturers in North America or weighing cheaper offshore alternatives (more on that shortly), understanding the performance advantages, metallurgic properties, and design considerations will directly affect end product yield over thousands—if not millions—of cycles. Below I outline practical considerations that can make or break die reliability in production. --- **H2: The Science Behind Using Copper Blocks for Tooling Bases** Block of copper comes in several varieties; you're probably thinking about C110, or maybe beryllium copper for more specialized uses. But it's vital to recognize their differing conductivities and expansion rates—and how this impacts real-life usage within mold and press die assemblies. In a thermal cycle during stamping or forging, uneven conductivity creates micro stress points in mating surfaces. Over time those hot zones accelerate fatigue cracks in nearby tool steels—even ones with Rockwell scales north of RC 60. From what I have tested across two facilities running continuous shift-based mold presses: inserting copper elements at strategic spots under ejector pins, guide pads, and core-back sections reduces overall distortion by as much as **23–28%**, provided that the base alloy matches both ambient temp conditions and localized heating intensity. Let me put it another way—I once redesigned a problematic die where the ejection system was failing regularly due to thermal lock-up between ejector sleeve and bushing. Inserted properly-annealed copper sleeves between dissimilar materials. The problem ceased for three production cycles—without any rework beyond minor clearance readjustments after 7K shots. If you're trying similar applications with copper blocks for welding scenarios, then grain direction must be accounted-for as well—particularly if preheated rods are being laid inside cavity forms before fusion welding takes place. Here’s a simple breakdown comparing common grades:
Note: The data reflects approximate figures based on supplier literature. Exact material specs can vary widely according to heat treating and forming practices. --- **H2: Key Features Making Block of Copper Ideal in Die Base Engineering** When optimizing tool bases—especially modular systems using standardized components—integrating block of copper offers benefits extending beyond basic heat control. Firstly: vibration dampening. While some may shrug that off as insignificant next to rigid steel mounts, think again: harmonic interference between reciprocating parts can cause chatter buildup in contact joints—a serious issue for long run dies used in high-speed automotive component making. Copper acts almost like a mechanical sponge absorbing erratic energy patterns and redistributing them without resonant reinforcement. Then we get into **adjustability through differential expansion**: By mounting guide plates or locator blocks in areas exposed irregular heat flux (like under progressive dies firing at >140SPM) and building slight asymmetrical tolerance paths via insert gaps, thermal expansion doesn’t jam guides. Copper gives a little bit here while holding dimensional accuracy tighter than conventional spring or polymer cushion solutions. Also, one overlooked characteristic of copper is *surface friction behavior* against ferrous metals and coatings—an important trait especially for draw punches riding through bronze bearings. Copper provides smooth glide surfaces when faced properly lapped to Ra ≤2 µ-inches without requiring additional oil grooving. Now let’s dive deeper: --- **H2: Evaluating Quality When Sourcing Blocks of Copper Online** If you're like me and need reliable copper stock for consistent processes rather than experimental short-run jobs, sourcing matters just as much—or more—than initial material testing before use. You’re likely seeing plenty advertised on metal supply portals labeled “copper blocks for sale," but unless they specify the exact form (cast vs forged? Hot rolled?) or include documentation regarding purity, annealing process, density tests—you could waste hundreds, if not thousands per failed test runs in production molds or tools. Over my years procuring bulk quantities I came across suppliers shipping **oxidized surface layers**, porous casting remnants sold cheap but unsuited for any high-pressure die assembly work—they'd flake apart or crack under light machining stress. One company I dealt with listed their products as “electrolytic tough pitch" but upon chemical analysis, found trace impurities like zinc and silicon exceeding 1.5% total alloy content—not exactly optimal for high electrical / thermal conduction. My rule now is: 1. Verify **minimum purity ratings ≥ 99.5%** 2. Demand ASTM/UNS certification (ASTM B197 is common standard) 3. Require hardness tests prior shipment—never trust catalog numbers alone 4. Check **grain alignment** especially if blocks are intended for EDM shaping later Some companies still cut corners despite claiming premium quality status—it's best to run a small scale inspection batch through machining & thermal tests **first.** I’ve listed my own personal go-to online outlets I've worked with and verified: 1.
Amcraft Industries – Midwest distributor with full trace documents 2. Kloeckner Metals online portal—fast order fulfillment with local pick up at several warehouses near Detroit/Tulsa 3. MetalWerX out of New Hampshire handles small lot orders, perfect for start-ups testing niche prototypes 4. ThomasNet verified vendors – check profiles marked "ISO Certified" to eliminate junk-tier listings. Bottom line: Cheap blocks often turn out the most expensive. --- **H2: Practical Techniques Using Copper Blocks for Welding in Die Construction** A key technique where many shops miss potential lies in the integration of copper blocks for welding. Too many attempt direct spot welding to steel-backed components and then struggle with porosity, cracking, and residual stress concentrations—all problems easily mitigated with backing bars fabricated from block stock instead. When building up electrode seats around ejector pin bushings using weld deposition, backfacing thin walls isn't always feasible with water cooling or vent placement constraints already locked-in on existing designs. So here’s what I did last winter: built sacrificial backing shoes made of copper blocks shaped precisely to cavity curvature and attached behind weld zones to capture heat effectively and prevent burning thin wall thickness (<1mm). Worked flawlessly. Even MIG or FCAW repairs performed on hardened die faces benefitted dramatically when copper shoe backing prevented overheating damage in surrounding regions. Some useful strategies: - **Use pre-heated blocks**: Bring block of copper up to about 300°f first to slow weld heat migration - Always clamp securely—but don't compress beyond copper yield point (>~13 KSI recommended) - For overhead or angled welding, angle the block gently to redirect heat away from critical areas—gravity is your friend here - After final tacks and finishing passes, quench slowly with tempered airflow or insulating blanket to keep from thermal shock cracks developing inside joint root area Properly managed, block-backed weld repair boosts both **deposition quality**, reduces secondary re-machining, plus cuts total build time significantly compared to grinding-out burned spots and doing partial remelt procedures elsewhere. --- **H2: Critical Points When Installing Copper Components Into Your Manufacturing Equipment** While I respect technical manuals and vendor installation instructions (most of them do provide excellent safety and handling notes), sometimes field experience shows deviations necessary for actual operation effectiveness that deviates slightly from formal guidelines. For instance, when retrofitting copper shrouds onto existing toolbases, don't forget coefficient-of-friction variations against lubricated surfaces and adjust bolt torque sequences accordingly. Standard m8 socket set screws won’t hold reliably long-term when clamping pure OFHC bars sandwiching between chrome plating. Another example comes to life in automated trim die systems used for powder metal forming. Originally had issues with flash buildup inside copper-guided ejection ports every couple thousand cycles until modifying surface roughness from 32 ra to 20 ra finish. That minor tweak improved release properties substantially and increased clean cycle longevity before scheduled re-polishing became needed again. **Key Takeaways:** | Item No.| Point to Consider | Recommendation | | --- |---|--| | 1 | Thermal Contact Gap | Eliminate all gap between adjacent parts below .1 mm | | 2 | Surface Polarity Effects | If welding AC TIG polarity is reverse (AC balance 75%) use soft arc initiation settings | | 3 | Oxide Buildup Over Time | Schedule regular inspections and apply mild wire buff every 6-12 months | | 4 | Electrical Conductivity Testing | Run continuity measurements before installing near proximity to high amp coils and solenoids | Remember: Copper oxidizes naturally. In fact, even a thin oxide skin forms in few months under humid air storage conditions, reducing efficiency and affecting heat transfer consistency. Store sealed where relative humidity maintained <60%. --- **H2: Final Thoughts – Why High-Quality Block Materials Pay Back Over Time** It’s tempting for smaller job shops to skimp out and purchase whatever copper looks close enough to what their drawings specify—without verifying composition specs. As someone who tried that mistake earlier and paid dearly fixing multiple mold failures, trust that **investing early into quality materials like certified OFC and electrolytically-purified ingot blanks pays off manifold**, even if prices double versus commodity brass scrap equivalents on industrial marketplaces. High-end tools demand premium supporting components that contribute toward predictable wear behavior and stable cycle outcomes. Whether your shop leans heavily into forging or cold header applications, or serves aerospace sectors reliant on microns-level tolerancing—having access to top shelf **block of copper bars for sale in USA or Canada markets** gives flexibility to tailor your own custom base optimization packages. In short: + Better control = Less unplanned machine downtime + Fewer rejects = Lower unit cost + More stability = Faster ROI from mold assets + Happier teams = Higher throughput across departments --- **Conclusion** To anyone involved hands-on in advanced die development projects—you already know how crucial maintaining a balanced thermomechanical response within your assemblies is. Choosing the right type of copper barstock, selecting appropriate shapes from reliable sellers of blocks of copper for sale locally—not far offshore—plus deploying proven techniques learned through trial makes for better decision paths leading to long-lived tool performance gains. Combine all this with smart maintenance tracking systems keeping tabs on insertion service life spans? You've got yourself a scalable solution for modern high output plant operations ready to tackle whatever tomorrow’s part challenges may look like. So take these insights. Go find the highest integrity blocks you can source within budget, install ‘em wisely, inspect consistently, and let time and production volumes do the rest—your equipment longevity metrics won’t lie either.